Ultrasonic testing of electrical equipment valve steam leak detection
Ultrasonic testing of electrical equipment testing valve class and condensate valve leak detection equipment to detect electrical mechanical bearing detection ultrasonic detection valve type and condensate valve leak detection of mechanical bearing detection
Heat exchanger, boiler and condenser ultrasonic detection, ultrasonic detection of ultrasonic detection of aircraft, ship, automobile transportation industry, ultrasonic detection, ultrasonic detection of compressor, mechanical operation of ultrasonic detection,
超声波检测电气设备检测阀门类与凝汽阀泄漏检测轴承机械检测超声波检测电气设备检测阀门类与凝汽阀泄漏检测轴承机械检测
热交换机、锅炉及冷凝器超声波检测,航空器超声波检测,船舶超声波检测,汽车运输行业超声波检测,压缩机超声波检测,机械运转超声波检测,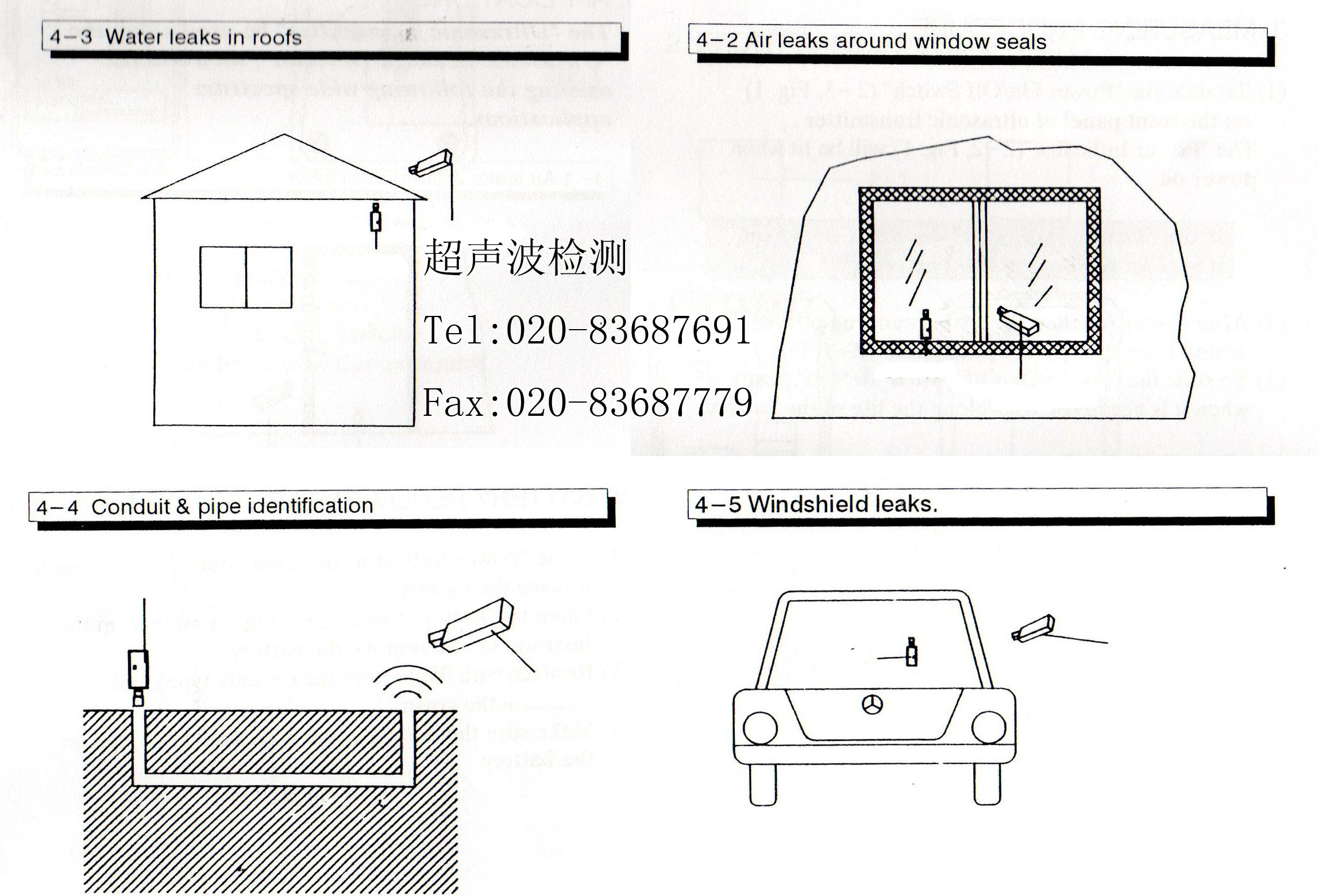
Ultrasonic testing service
Application
(1) the refrigerator air system leakage
The instrument can leak detection refrigerator vacuum or pressure type of leak and air conditioning system during installation. When the refrigerant leakage when the leak will produce ultrasonic, using the detector can accurately find the leak location.
(2) heating system leakage
(3) vapor transmission system leakage
(4) the compressed air leakage
(5) the tyres and the pipeline leakage
(6) engine sealing
(7) arc
Arc produces ultrasonic rich bandwidth it can also be detected.
(8) the pressure test
(9) drying system
Using the detector + ultrasonic generator
(1) the door and window seal check
(2) the roof Water Leakage
(3) the ditch pipeline screening
(4) the door seal
(5) the cab wind
Application of ultrasonic detection of various industries
1 ultrasonic leak detection
Ultrasonic leak detection application is extremely extensive, almost all the factories are available. No matter what types of fluid leakage, leakage can be detected, the more serious, the stronger the signal, especially suitable for the saturated gas, many gas, pressure vessel, vacuum processing applications.
Detection of electrical equipment
When the switching device, transformer, insulation device, circuit breaker, relay, busbar electrical discharge occurred, such as arc, leakage or corona, may be a potential fault. This signal sounds like fried buzzing or humming sound, the more close to the discharge, the louder the sound. With the use of accessories (ultrasonic wave collector) to detect the overhead power line.
Detection of class of the valve and steam trap
When the fluid (gas or liquid) from the high pressure end through the valve to the low end, will be relatively "An Jing" under normal circumstances, once the valve or blockage, the liquid through the leak point or block segment, it will produce turbulence. Turbulence will produce ultrasonic signal is strong, and even in the noise environment can also be detected.
Manufacturing plant steam traps most are recommended to ultrasonic detection method is the most reliable. Condenser valve leakage is too large or obstruction, can be easily measured. Instrument FM function can highlight the fault signal, interference significantly reduce the foreign sound, even if the detection of arrangement of a plurality of condensing steam valve close is not affected.
Bearings and mechanical parts detection
In the early fault found abnormal. Can be found in bearing and oil bearing a foreign body in excess, and serious abrasion in various speed, ultrasonic HF can avoid deviation, filter out background noise, and in the condition of vibration using is not affected.
The sound signal of mechanical motion can produce wide frequency, small changes can be very sensitive to the detection of acoustic amplitude and pitch in the high frequency narrow band, may carry on the contrast, can also be observed the change tendency. According to the NASA research, higher than that of 8dB indicates the lack of oil, higher than 12dB indicating fault early period, 16dB above means that the fault has been developed, 35-50dB is the accident forecast.
Heat exchanger, boiler and condenser detection
These devices available detection pipe, tube plate and the box body. There are three kinds of method for detecting leakage: pressure, vacuum and ultrasonic testing. Pressure and vacuum testing, ultrasonic receiving the leak point is issued, and ultrasonic testing, is a special acoustic generator in the box body, the ultrasonic signal is transmitted to the pipeline, the ultrasonic signal and then leak out from the external detection instrument, suitable for with part load repair or maintenance shutdown.
Aircraft detection
System of aircraft, such as compressors, valves, power, pump, cabin windows and so on, will produce ultrasonic, some from the turbulence, some from the friction. When these parts begin to wear, failure or leakage, ultrasonic can produce abnormal. The first scan mode in ultrasonic detector to find the abnormal sound diagnosis and contact mode region.
Ship detection
Application of ultrasonic detection in the shipbuilding industry is very extensive. In the sealing waterproof board, hatch covers, condenser, steam system, compressed air system, all kinds of mechanical parts and all kinds of valves etc.
. In the absence of the pressure of circumstances, can be used in conjunction with the ultrasonic generator to detect the sealing performance of the corresponding equipment.
Application of transportation industry
The general scope of application of water sealing, wind noise, pneumatic brake, radiation leakage etc.. According to the traditional methods, the use of hose and flash detection of leaking and wind noise, time consuming and poor accuracy. Using soap and blister test of air brake and radiation leakage, is time consuming and inefficient. The use of ultrasonic testing is much more relaxed. The ultrasonic generator is placed in the cabin (body), scanning the door, window, floor, the seal, can accurately, quickly and easily complete the detection.
The compressor test
Compressor is the heart of gas compression system, even small leaks will also expand rapidly, threatening the security of the system. Ultrasonic testing for detection of two kinds of method of compressor valve. One is the "direct" method, contact valve for probe, and then adjust the sensitivity of the instrument to determine the most strong voice. Another method is through the attached to the metal surface of the magnetic seat "detection. The magnetic seat can eliminate the mechanical vibration effect to instrument reading
Mechanical operation detection
Students a wide range of sound mechanical operation process, only focus on the HF portion receives them, and detect the acoustic amplitude and sound quality of the subtle changes in. Through the "heterodyne" ultrasonic received signal into a sound signal ear audible range, so it can be observed through the instrument, use the headphones, and state monitoring for mechanical equipment.
Application of ultrasonic detection of rail transportation in railway contact net
The electrified railway traction power supply
Electric railway traction power supply proposal
An industry overview:
All kinds of faults in electric railway catenary equipment, electrical burns because of its difficult to find fault in advance and harm is big, has aroused more and more attention of power supply operation maintenance department. In the electrified railway contact net, equipment is working in the dual role of force and power down, so the mechanical failure and electric burn fault form the subject of catenary fault. In the operation of the contact net for many years, traction capacity increases unceasingly in the situation, the phenomenon of electric burn equipment has become more and more prominent, and the problem of electrical burn in advance and not easy to find, very dangerous. Therefore, the prevention and control of the equipment contact net electrical burn occurs fault has become the power supply operation unit is an important task to ensure the security of electricity supply.
Current electric railway industry detection means:
Contact net is a kind of special power supply equipment. Because of its special structure and conditions of use, its fault is also a variety of. The fault phenomena, the causes and should study measures will help strengthen the understanding of the origin of the fault, and constantly improve the technology and means of detection, currently in the electrified railway traction electrical detection mainly infrared thermometry based, but encountered this detection mode, there are many problems, has brought some inconvenience to the detection work daily.
Analysis of the causes of failure problem of electrical burn:
In the electrical design, although the line traction capacity to increase margins have been considered, but with the development of railway transportation, to increase the traction capacity now is beyond the margin. The long run some clues for the continuous carrying capacity is too small to bear a large current, electrical burn occurs.
The contact network leading electric back feeder, separated separated routing, lead, catenary, contact wire, electric connector, suction, suction change variable lead etc.. Between the various parts are connected by a variety of wire clip, make this a loop along the railway extension, satisfy the need of power supply to the electric locomotive. The main circuit current must be good, can guarantee the smooth; if flawed, will cause the local load through the large, serious parts shunt, which burns contact line equipment.
Electrical, chemical corrosion and electrical connection part due to bad connection or long time running loose, resulting in cross section of main circuit (or equivalent cross-sectional area) is insufficient, the electrical connection impedance increase, thus guide is not smooth, burn the contact line equipment. Such as: the bearing cable into the electric connector and electrical part of diversion; electric connection clamp size slot against; clamp with debris; equipment wire clamp of non face to face contact etc..
Connecting clamp burn
The structure of the contact network station is more complicated, in electrical connection, due to various reasons resulting in the main circuit is not closed, the leading electric circuitous route, causing serious burns shunt catenary components.
Through some should not have current contact network structure design in place, but due to certain conditions by the coincidence of all or part of the traction current. Because these places is no guarantee of traction current (or shunt) through the necessary electrical connection, so burn catenary equipment.
Clues, clues and support device of the interchange between the line impedance is formed due to different voltage difference, in the wind, temperature and vibration and other factors, the distance between them is not enough, resulting in the discharge phenomenon, the discharge arc burn the contact line equipment.
The two ends of the in-phase and belongs to different feeder of the insulated section joint, sectional insulator, due to impedance power supply arm formed in different voltage difference, when the electric locomotive pantograph short connected by two power supply arm in a short moment, arcing contact, equipment caused by burn.
And yet in the construction is not strictly implement the relevant standards, causing the junction line electric connector is not correct, clamp installation is not standard. Overhaul regulation on electrical current standard electrical connection without quantitative indicators, which makes the power sector unsystematic in specific maintenance "". The electrical connection of the lack of effective methods and means of detection, in particular overhaul in doing some appearance inspection. The existence of "misunderstanding oiled" area. In order to prevent the equipment maintenance quality inspection points, maintenance staff a lot of butter smeared on the contact network equipment in peacetime maintenance, causing the internal electrical burn defect of equipment cannot timely discovered. Such as: to prevent the electric connection points in electric connection resistence, wipe the surface coated with a thick layer of butter. The equipment inspection especially vigil work ineffective implementation.
All electrical devices such as not to advance in the prevention of accident consequences:
The electric connecting clamp fever. The reason is the electric connection clamp did not press formulary installation or in the operation process of bolts loosening, electrical Compound Grease aging defects, make the electric connection point of the increase of contact resistance and heat increases, the wire clamp heat burn clues, severe cases burned clues.
The clue (contact wire, bearing cable, power supply line and return line, electrical connection part of self suction line) strand broken or disconnected.
The reason is the station track electrical connection set the position or number is not reasonable, the track between contact suspension flow taking in locomotive produced under the condition of large pressure difference across the contact suspension in soft produce circulation, resulting in pulling injury phenomenon in the weak links of electric discharge suspension pulley or locator root.
The equipment wire clamp, a joint clamp, suck choke is connected on-line with burns. Soft cross circulation caused by bearing cable suspension pulley or locator root positioning hook burns. Because of different suspension ask non stability of contact will cause the clue asked discharge: when 2 different suspension
超声波检测服务
应用
(1) 冰箱空调系统泄露
仪器可以检测冰箱真空或压力型泄露和空调系统安装时的泄露。当制冷剂泄漏时泄漏处会产生超声波,利用检测器可以准确找出泄露位置。
(2) 供热系统泄露
(3) 蒸汽传输系统泄露
(4) 压缩空气泄露
(5) 轮胎和管道泄漏
(6) 引擎密封
(7) 电弧
电弧会产生丰富带宽的超声波因此也可被检测。
(8) 耐压检测
(9) 烘干系统
使用检测器+超声波发生器
(1)房门及窗户封密检查
(2) 屋顶漏水
(3)水沟管道甄别
(4) 房门密封
(5)驾驶室防风
各行业应用超声波检测
1超声波泄露检测
超声波泄露检测应用极为广泛,几乎所有工厂都可用到。不论何类流体产生泄露,都能检测到,泄露越严重,信号越强,尤其适合于饱和气体、多种气体、压力容器、真空处理等应用场合。
电气设备检测
当开关装置、变压器、绝缘装置、断路器、继电器、母线排等发生电气放电,例如电弧、漏电或电晕,可能是潜在故障。这种信号用听起来像是油炸声或嗡嗡声,越靠近放电处,声音越大。配合使用附件(超声波集波器)可对架空电力线进行检测。
阀门类与凝汽阀的检测
当流体(气体或液体)从高压端通过阀门到低压端,在正常情况下会相对较“安静”,一旦阀门有泄露或阻塞,液体通过泄露点或阻塞段时,就会产生湍流。湍流会产生强烈的超声波信号,而且即使在噪音环境下也能被检测出来。
大部分的凝汽阀制造厂都建议超声波检测法最为可靠。凝汽阀漏气太大或阻塞,都可轻易地测出来。仪器的调频功能可突出故障信号,明显降低外来声音的干扰,即使检测排列紧密的多个凝汽阀也互不受影响。
轴承与机械部件检测
可在故障早期发现异常。在各种转速下都能发现轴承缺油和用油过量、轴承内有异物、磨损严重等,高频短波的超声波可避免偏移、滤掉背景噪声,且在振动情况下使用不受影响。
机械运动可产生宽频率的声音信号,在高频窄波段可以很灵敏地探测声波振幅和音调的微小变化,可进行对比,也可观察其变化趋势。根据美国宇航局的研究,高于8dB预示缺油,高于12dB表示故障初发期,16dB以上意味着故障已经发展了,35-50dB则是事故发生的预告。
热交换机、锅炉及冷凝器检测
可用检测这些设备的管道、管板和箱体。有三种方法检测泄露:压力、真空和超声波测试。压力和真空检测,是接收泄露点发出的超声波,而超声波测试,则是在箱体内放一个特殊的声波发生器,将超声波信号传送到各条管道后,再用仪器从外部检测漏出来的超声波信号,适合于带部分负载检修或停产检修。
航空器检测
航空器上的系统,如压缩机、阀门、动力、泵、座舱窗户等等,都会产生超声波,有的源于湍流,有的源于摩擦。当这些部件开始磨损、失效或泄露,产生的超声波就会异常。首先在超声波检测器的扫描模式下找到声音异常区域,再用接触模式进行诊断。
船舶检测
超声波检测在船舶工业上应用也很广泛。在防水板、舱盖的密封性,冷凝器、蒸汽系统、压缩气体系统、各种机械部件以及各种阀门等
。在没有水压的情况下,可以配合使用超声波发生器来检测相应设备的密封性。
运输行业应用
一般应用范围有水封、风噪音、气动刹车、辐射泄露等。按照传统方法,使用水龙带和闪光灯检测漏水和风噪音,费时而且准确性不佳。采用肥皂和水泡检测空气刹和辐射泄露,也是耗时低效。使用超声波检测则轻松多了。将超声波发生器放在舱体(车体)内,扫描门、窗、地板、封口处等,可以精确、快速而且简便地完成检测。
压缩机检测
压缩机是气体压缩系统的心脏,即使微小的泄露也会迅速扩大,威胁系统安全。超声波检测有两种方法检测可压缩机的阀门。一种是“直接”法,用探头接触阀门,再调整仪器灵敏度来判断声音最强点。另一种方法是通过附着在金属的表面的“磁座”检测。磁座可以消除机械振动过大对仪器读数的影响
机械运转检测
机械运转过程中生范围广泛的声音,仅专注于接收其中的高频短波部分,并探测其声幅和音质的细微变化。通过“外差法”将接收到的超声信号转化为人耳可听范围内的声音信号,这样就可以通过观察仪表,用耳机收听,进而对机械设备的状态进行监测。
超声波检测在铁路接触网轨道交通的应用
电气化铁路牵引供电建议方案
一.行业概述:
在铁路电气化接触网设备的各类故障中,电气烧伤故障因其事前难以发现而危害性又大,已越来越引起供电运营检修部门的重视。在电气化铁道中,接触网设备是在力与电的双重作用下工作的,所以机械故障和电气烧伤故障构成了接触网故障的主体。在接触网运行了多年、牵引运能不断增加的情况下,设备的电气烧伤现象已越来越突出,而且电气烧伤问题在事前又不易于发现,危害性很大。因此,在预防和防治接触网设备发生电气烧伤故障已成为供电运营单位为确保供电安全的一个重要任务。
目前电气化铁路行业检测手段:
接触网是一种特殊的供电设备.由于其结构和使用条件的特殊性,其故障也多种多样。对其故障现象、原因和应采取措施的研究有助于加强对其故障本源的认识,不断提高技术和检测手段,目前在铁路电气化牵引电气检测方面主要以红外线测温为主,但这种检测方式遇到的问题也非常多,给日常的检测工作带来了一定的不便。
电气烧伤故障问题原因分析:
① 在电气化设计中,虽对线路牵引运能的增加裕量有所考虑,但随着铁路运输发展,现在牵引运能的增加已超出了裕量。原采用的一些线索因持续载流量偏小而承受不了大电流的长期运行,就发生了电气烧伤。
② 接触网主导电回路由馈电线、隔开、隔开引线、承力索、接触线、电联接器、吸变、吸变引线等组成。各部分间由各种线夹进行连接,使这一回路沿铁路延伸,满足向电力机车供电的需要。主导电回路必须良好,才能保证电流的畅通;若存有缺陷,将引起局部载流过大、零部件分流严重,从而烧伤接触网设备。
③ 电气联接部分因连接不良或长时间运行松动等原因引起的电、化学腐蚀,造成主导电回路的截面(或当量截面积)不足,电气连接阻抗加大,从而导流不畅,烧伤接触网设备。如:将承力索纳入了电联接器电气导流的一部分;电联接线夹大小槽装反;线夹内有杂物;设备线夹间非面面接触等等。
连接线夹烧伤
④ 站场中的接触网结构比较复杂,在进行电气连接时,由于种种原因造成主导电回路不闭合、主导电通道迂回,引起分流严重而烧伤接触网零部件。
⑤ 设计的接触网结构中某些不应有电流通过的地方,而由于某些条件的巧合通过了全部或部分牵引电流。由于这些地方没有保证牵引电流(或其分流)通过的必要的电气连接,所以烧伤了接触网设备。
⑥ 立体交叉的线索、线索与支持装置间,由于线路阻抗的不同而形成电压差,在风力、温度变化、振动等因素的作用下,它们之间的距离不够,造成放电现象,放电电弧烧伤了接触网设备。
⑦ 两端属同相而不同馈线供电的绝缘锚段关节、分段绝缘器,因供电臂的阻抗不同而形成电压差,当电力机车通过受电弓短接两供电臂瞬间,在短接点处产生电弧,造成设备的烧伤。
⑧ 然而在施工时未严格执行有关标准,导致电联接器的结线不正确、线夹安装不标准。现行的检修规程中对电气联接的电气标准没有量化指标,使得供电部门在具体检修时“无章可循”。对电气联接缺乏行之有效的检测方法和手段,在具体检修中多是做些外观上的检查。工区存在“涂油”的认识误区。为防止设备检修质量验收时扣分,检修人员在平时检修时对接触网设备抹涂大量的黄油,致使设备的内部电气烧伤缺陷不能及时地被发现。如:为防止电联接散股扣分,在电联接表面抹涂上一层厚厚的黄油。对设备的巡视特别是夜巡工作执行不力。
各种电气装置如不提前预防事故的发生造成的后果:
① 电气连接线夹发热。原因是电联结线夹未按规定安装或在运行过程中发生螺栓松动、电力复合脂老化等缺陷,使电联结处接触电阻增加进而发热量增加,使线夹发热而烧伤线索,严重情况下烧断线索。
② 线索(接触线、承力索、供电线、回流线、吸上线)自电气接续部分断股或断开。
原因是站场股道电联结设置位置或数量不合理,使股道间接触悬挂在机车取流的情况下产生较大的压差,接触悬挂在软横跨上产生环流,从而在悬吊滑轮或定位器根部等电气薄弱环节产生拉放电伤现象。
③ 设备线夹、接头线夹、吸上线与轭流圈连接处烧伤。软横跨环流造成承力索悬吊滑轮处或定位器根部定位钩处烧伤。原因是不同悬挂问非稳定性接触也会造成线索问放电:当2不同悬挂立体交叉时.如果2支悬挂均为载流悬挂.当其中1支有大负荷电流时,根据潮流计算可知,在2悬挂问会形成电位差,此时如果2悬挂问存在非稳定性接触,则在2悬挂问就会产生过渡电弧进而烧伤线索。此种情况一般发生在站场交叉承力索问和非支接触线与工支定位管问。
④ 通过以上故障原因分析接触网既然是机、电合一的特殊供电设备,因此在运行过程中不可避免发生电气方面的问题。电气方面故障虽数量不多,但一旦发生,则会造成严重影响,甚至造成塌网、断线故障。
好的检测手段和设备能起到故障早期预防和发生:
2003年-2004年全国牵引供电系统事故分析和解决方案:
2003年电气化铁路因为变电所故障所导致系统停电次数累计41次,停电1986分钟,停电平均时间为82分钟。2004年因为变电所故障停电次数为32件,停电902分钟,故障平均停电时间为68分钟,波及面和损失非常大。
针对牵引变电所的故障分析,可以采取以下措施来提高其供电可靠度:
① 采用超声波检测仪器,提高设备的运行可靠性。认真做好日常运行维护工作,提高设备健康水平,运行人员加强巡视维护质量,可以及时发现或消除设备隐患,提高供电可靠性。
② 全方位配合开展设备状态检修,利用绝缘在线监测、带电测试和超声波检测及红外热成像监测发热点等措施,加强对设备的监测工作。
2004年因接触网系统发生故障340件,累计停电31148分钟,故障平均停电时间为92分钟,占牵引供电系统故障的 91%;2004年因接触网系统发生故障停电274件,累计停电25160分钟,故障平均停电时间为92分钟,占牵引供电系统故障的95%。波及面和损失非常大。
针对接触网的故障分析,可以采取以下措施来提高其供电可靠度:
① 设计标准,如风速选值,最大受风偏移量,接触网最大跨距,锚段长度,下锚偏角,设计拉出值等技术参数都需要认真研究。
② 选用耐腐蚀的优质材料,采用表层防腐处理,定期清扫接触网。
③ 有计划地对接触网上的各个连接部位及线夹进行有效的实时监控,利用超声波检测仪及时发现线夹松动和绝缘损坏的早期放电现象,起到预防设备故障的发生。