Prefabricated cabin switch station photovoltaic 35KV24KV12KV6KV box substation
The 35kv24kv12kv modular prefabricated cabin substation can be configured as a container-type switch station, a photovoltaic booster station, a primary equipment cabin, and a secondary equipment cabin. The construction and installation are fast, the land is saved, and it can be built in multiple layers, generally up to 3 layers.
Widely used in photovoltaic power stations, wind power stations, substations, power plants, user engineering, energy storage projects,
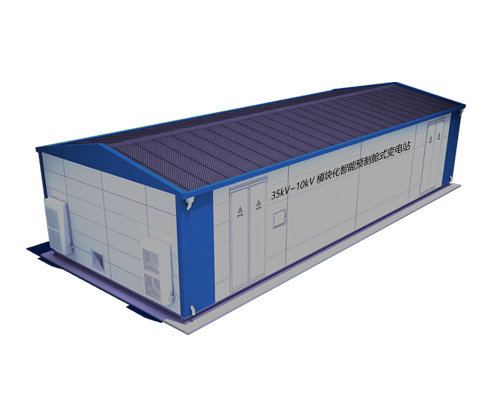
The 35kV~10kV modular prefabricated cabin substation is a transformer, multi-circuit high-voltage switch system, reactive power compensation device, insulated busbar, substation integrated automation system, communication, telecontrol, metering and DC power supply and other electrical units. , Reliability, easy maintenance, and integration principles are integrated and installed in a heat-insulating, fire-proof, anti-theft, moisture-proof, small animal-proof, five-sided ventilated, fully enclosed, and movable steel structure box. It is suitable for the construction and renovation of urban and rural 10Kv~35Kv integrated substations, small and medium-sized substations (distribution) substations, and substations of factories and mines. Because it goes deep into the load center, reduces the power supply radius, and improves the quality of power supply, it is especially suitable for urban distribution network transformation, and is known as "the target model for substation construction in the 21st century". It complies with the standards of the State Grid Corporation of China, the new rural electrification standard system and the electrification implementation outline. It has really realized the leap from building a substation in the traditional way to buying an integrated substation!
Features
■ The standard design of 35kV~10kV modular prefabricated cabin substation covers an area of only 230 square meters, which can save 60%~80% of the occupied area compared with conventional substations, which is in line with the national land saving policy.
■ The electrical equipment used can effectively reduce the product cost; the electrical equipment is installed indoors and will not be affected by external factors, and the operation and maintenance costs are greatly reduced; the all-metal structure shell is adopted, and all components have been treated with anti-corrosion treatment. Very small amount, long service life and low energy consumption;
■ The overall construction scheme is adopted. The conventional design scheme has been constructed many times. The design and construction are carried out according to the ready-made scheme, and the local adjustment is very small. The functional modules such as: incoming line module, outgoing line The protection module only needs to be called directly, and the production cycle is relatively short. The construction period is shortened to 3 months, while the construction period of conventional substations takes at least 1 year. It is really better to buy a station than to build a station.
■ The prefabricated integrated substation has almost no impact on the environment, because the amount of construction in the early stage is very small. Except for the structure, all construction work is carried out indoors, and the noise and electromagnetic radiation during operation are shielded in the metal layer. Moreover, the shell structure is all metal components, and its service life is much longer than that of brick-concrete and cement structures, and all parts can be recycled and reused.
Conditions of Use
■ Place of use: outdoors;
■ Altitude: ≤ 3000m;
■ Ambient temperature: -45°C ~ +45°C, the maximum daily average temperature does not exceed 35°C;
■ Wind speed: ≤ 35m/s;
■ Ground slope: ≤ 5;
■ Sunlight radiation: ≤ 1000W/m2;
■ Relative humidity: daily average ≤ 95%, monthly average ≤ 90%;
■ Thickness of ice coating: 10mm;
■ Earthquake cracking degree: no more than 8;
■ Foundation: the characteristic value of foundation bearing capacity Fak = 150kpa, without the influence of groundwater;
■ There is no danger of explosion, fire, chemical corrosion and severe vibration at the installation site.
■ Please contact our technical department if it exceeds the provisions of these conditions of use.
Prefabricated cabin structure and technical requirements
The overall structural design of the cabin body should comply with the requirements of the current national standards and design specifications, and in combination with the actual engineering, rationally select materials, structural schemes and construction measures to ensure that the structure meets the requirements of strength, stability and rigidity during transportation and installation, as well as waterproof and fireproof , anti-corrosion, durability and other design requirements.
The installation and arrangement of equipment in the prefabricated cabin shall meet the requirements of relevant regulations and specifications.
The bidder shall provide the structural design scheme of the prefabricated cabin, the selection of interior and exterior wall materials, the selection of electrostatic floor, the selection of air conditioning and ventilation and other specific design schemes, as well as the internal and external renderings and photos of the prefabricated cabin.
1. The importance factor of the cabin should be designed according to the safety level of the structure, and the design service life should be considered as 25 years. The protection level of the cabin should not be lower than the requirements of IP55 specified in GB/T 4208-2008.
2. The cabin body should adopt a steel structure system, the roof should adopt a cold-formed thin-walled steel purlin structure, the outer side of the enclosure structure should be made of functional and decorative maintenance-free materials, and the inner side should be made of lightweight, high-strength, water-resistant, anti-corrosion, Flame-retardant and heat-insulating panel materials, the middle should be made of materials that are not easy to burn, have low water absorption, and have good heat preservation and heat insulation effects.
3. The cabin body should adopt steel column structure, the main rigid frame can adopt solid web rigid frame with equal cross-section, and the support spacing between columns should be determined according to the longitudinal column distance of the box room, the stress situation and the installation conditions. When it is not allowed to set inter-column supports, other forms of support can be set; when no support is allowed, longitudinal rigid frames can be set. Rigid tie rods shall be arranged along the entire length of the cabin at the turning point of the rigid frame (side column top and roof ridge).
4. The lifting point of the cabin should be set at the bottom of the prefabricated cabin. The location and number of lifting points should be determined after detailed calculation according to the load distribution of the equipment in the cabin to ensure safety and reliability.
5. Structural self-weight, maintenance concentrated load, roof snow load and dust load, etc. shall be adopted according to the current national standard "Code for Building Structure Loads" GB 50009, and the suspended load shall be taken according to the actual situation.
6. The standard value of the wind load of the cabin should be calculated according to the provisions of Appendix A of CECS102 of "Technical Regulations for Portal Frame Light Steel Structures".
7. Earthquake action shall be calculated according to the current national standard "Code for Seismic Design of Buildings" GB 50011.
8. The skeleton of the cabin body should be welded as a whole to ensure sufficient strength and rigidity. The cabin should not be deformed or damaged during lifting, transportation and installation. The deformation of the cabin steel structure of the steel column structure shall be calculated according to the requirements of CECS102 in the "Technical Regulations for Portal Frame Light Steel Structures".
10. The cabin door setting should meet the equipment transportation and inspection requirements in the cabin. Class B fire doors should be used. The combustion performance and fire resistance of other building components should meet the provisions of Article 3.2.1 of the "Code for Fire Protection Design of Buildings" GB50016. Use fans and air conditioners to achieve ventilation.
11. The opening of the cabin body meets the requirements of the Fire Protection Code for Design of Thermal Power Plants and Substations (GB50229-2019). The door opening size meets the equipment handling requirements. In principle, the door is set at the end of the long side of the cabin, and the door opening position should be coordinated with the general layout.
12. The cabin body should adopt a double-slope roof structure, and the roof slope should not be less than 5%. In northern regions, the roof slope can be appropriately increased to prevent water and snow accumulation. The roof panels should be made of lightweight, high-strength, corrosion-resistant, and waterproof materials, and the middle layer should be made of non-combustible, low water absorption, low density and thermal conductivity, and thermal insulation materials with a certain strength.
13. The roof of the cabin can adopt two ways of organized drainage and natural drainage. When the organized drainage is adopted, the drainage tank and the downpipe shall be supplied together with the cabin body and shall be installed on site, and the downpipe shall be built-in. Scattering can be used for cold regions. The air-conditioning drainage pipe should adopt the method of concealed laying or groove box concealed laying.
14. Checkered steel plates or epoxy resin partitions can be used for the bottom plate. The floor of the cabin should adopt ceramic anti-static raised floor, and the steel bracket of the raised floor should be fixed on the bottom of the cabin. The height of the anti-static raised floor should be 200-250mm, which should be convenient for cable laying and maintenance.
15. The cabin and the foundation should be firmly connected, and should be welded to the embedded parts of the foundation. Weather-resistant silicone glue should be used to seal the joint between the cabin and the foundation to prevent moisture from entering.
16. The 35kV switchgear is placed in the box along the length of the prefabricated cabin, and two channel steels (above #8) are arranged along the bottom plate of each row of screen cabinets, which are welded with the bottom plate as the installation basis of the switchgear, and the chassis of the switchgear is passed through the anchor bolts Fixed with channel steel, bolt specification M12 and above.
17. Effective anti-corrosion measures must be taken for the cabin structure, and the structure should be convenient for inspection, cleaning, painting and avoiding water accumulation. After anti-corrosion treatment, there should be no metal matrix corrosion after at least 196 hours of neutral salt spray test.
4.9.4 Requirements for configuration of electrical and auxiliary facilities in prefabricated cabins
1. Complete safety protection, fire alarm and video surveillance measures should be set up in the prefabricated cabin, and lighting, maintenance, grounding, etc. should be set at the same time to ensure the safe operation of the prefabricated cabin equipment and personnel inspection requirements.
2. The lighting in the cabin should meet relevant regulations and specifications such as "Technical Regulations on Lighting Design of Thermal Power Plants and Substations" DL/T 5390, "Architectural Lighting Design Standards" GB50034, "Code for Design of Low-Voltage Power Distribution" GB50054, "Fire Emergency Lamps" GB17945, etc. requirements.
3. The design of the fire detection and alarm system in the prefabricated cabin and the fire control equipment and their functions shall comply with the current national standard "Code for Design of Automatic Fire Alarm System" GB50116. The cabin should be equipped with fire alarm and smoke detection devices. The fire alarm smoke detection device adopts the ceiling arrangement. Portable fire extinguishers should be equipped in the cabin and placed at the door. The level and quantity of fire extinguishers should be configured according to the fire hazard category as medium risk. When safety and reliability are ensured, a fixed gas fire extinguishing system can be installed. The bidder needs to cooperate with the acceptance of the local fire department.
4. Heating and ventilation facilities such as air conditioners and fans should be installed in the cabin to meet the requirements of the equipment operating environment. Under normal working conditions, the temperature in the cabin should be controlled within the range of (5-30) °C.
5. The cabin should be equipped with a mechanical ventilation device to form a ventilation circuit in the cabin. When fans are used for ventilation, the air duct should have dust removal and waterproof measures, and positive pressure ventilation should be used to prevent dust from entering the cabin during ventilation.
6. The relative humidity in the cabin is 45% to 75%, ensuring that the equipment does not condense under any circumstances.
7. Video monitoring should be installed in the cabin, and 2 Hikvision network cameras are installed in the cabin, which are connected to the video monitoring system of this project.
8. At least one distribution box is installed in the cabin.
9. An emergency escape door should be installed in the cabin, which can be activated in any case. The rest of the doors shall meet the requirements of relevant specifications.
4.9.5 Cable interface requirements for prefabricated cabins
1. The cables are directly led from the cabinets in the cabin to the outside of the cabin, and there is no centralized cable interface cabinet.
2. The prefabricated cabin adopts the downward routing method. The bottom of the cabin needs to be equipped with a control cable box or interlayer, and the height should be 200-250mm. The cable laying and cable arrangement follow the conventional cable laying regulations.
3. The prefabricated cabin should be in accordance with the requirements of the civil engineering design and the cooperation with the primary equipment, and the cable entrance and exit should be reserved;
4. The external prefabricated cable and the box, and the equipment interface between the boxes should meet the enclosure protection level IP54.
4.9.6 Grounding and anti-interference requirements for prefabricated cabins
1. The prefabricated cabin and its internal equipment complete working grounding, protective grounding, lightning protection grounding, and anti-static grounding in the station. The grounding system of the prefabricated cabin shall meet the requirements of GB/T 50065-2011 "Code for Grounding Design of AC Electrical Installations".
2. The main grounding line should be concealed in the prefabricated cabin. Each prefabricated cabin should be provided with 2~4 temporary grounding terminals at a distance of 300mm from the access floor. The grounding terminals should be copper bolts with a diameter of not less than 12mm. An obvious primary grounding mark shall be set at the connection point.
4.9.7 Material requirements for prefabricated cabins
1. The prefabricated cabin wall adopts thermal insulation composite wall. The prefabricated cabin wall is composed of outer wall (Jinbang board or facing FC board), polyethylene moisture-proof sealing film, thermal insulation material, keel frame, inner wall (aluminum-plastic board or clip Core board) and other materials.
2. The material of the steel column structure cabin should be composed of painted FC board, polyethylene moisture-proof sealing film, thermal insulation material, European pine board, structural components, aluminum-plastic board and other materials from outside to inside.
3. The material of the internal structural parts is required to have good compatibility with the welding (connection) of the main body of the box, high reliability, beautiful surface and no corrosion.
4. The insulation material should be rock wool or polyurethane, and the thickness of the insulation material is determined according to the thermodynamic simulation calculation.
4.9.8 Cabin interior and exterior decoration requirements
1. The name of the prefabricated cabin is spray-painted on the front of the outer facade of the cabin, and the group LOGO is printed in the upper left corner. The name of the prefabricated cabin shall be named according to the function, and shall be centered at about 2/3 of the total height of the bottom of the outer wall and bilge in the length direction of the prefabricated cabin. The font shall be black and bold, with a height of 500mm. The LOGO of the integrated manufacturer shall be marked on the lower left corner of the white area on the lower part of the outer wall in the width direction of the prefabricated cabin, and the height shall not exceed 150mm.
2. The appearance form and color of the screen cabinets in the cabin should be unified, and the position, font and height of the screen cabinet name and manufacturer name should be consistent.
4.9.9 Layout requirements for prefabricated cabin screens
The 35kV switchgear in the prefabricated cabin shall be arranged in a single row.
Machining center, can be processed and custom-made, custom-made, custom-made, custom-made, custom-made box | shell/wind power box shell/environmental protection/desulfurization/denitrification/stainless steel dust collector box/, power plant, factory, special tank for high-rise buildings Body box shell, processing carbon steel and other metal products sales, to provide customers with the highest quality, most comprehensive and personalized "one-stop" metal sales service. The stainless steel products we operate cover 200, 300, 400 series, with complete varieties and specifications.
Excellent processing and distribution of equipment, providing non-standard products such as slitting, flat plate, shearing, forming, frosting, 8K mirror, 6-meter bending, rolling and other surface treatment, laser cutting, punching, welding and other surface treatment, sheet metal forming, etc. Deep processing, all-weather distribution, one-stop service. It can meet the various needs of each customer and provide customers with "personalized" high-quality processing and distribution services
My company processing center, processing of stainless steel plate, stainless steel coil, stainless steel pipe and stainless steel products and professional stainless steel; carbon steel and other metal products processing camp sales, as customers
Metal sales service for the best quality, most comprehensive, personalized "one-stop". Management of stainless steel products cover 200, 300, 400 series, variety, specifications are available.
Equipment excellent processing and distribution, provides the strip, plate, shear compression, molding, grinding, 8K mirror 6 meters, bending, pressing circle cutting, laser cutting, punching, welding, surface treatment of sheet metal forming
And other non-standard products deep processing, all-weather distribution, one-stop service. To meet the different needs of each customer, provide for the customer "personalized" high quality processing, distribution services
Flat strip
The precision plate machine can be divided into strips and plated at the same time, and can process stainless steel, aluminum plates and other plates with a thickness of 0.3mm-3.0mm and a width of 200mm-1600. The straight dimension can be accurate to 0.3mm, it can be attached with paper and film, the diagonal line is accurate, the board surface is straight, and it has a super long discharge rack. The longest straight dimension of a single piece can reach 10 meters. Two production lines with a full load of 500 tons/day
The precision slitting machine can process stainless steel, aluminum and other plates with a thickness of 0.3mm-3.0mm and a width of 200mm-1600mm. This machine winds and expands the tube seamlessly, which can be laminated with plastic on one or both sides and divided into strips, meeting the requirements of fine and high standards. Maximum line speed: 250m/min
But while strip side plate precision flat machine, capable of processing 0.3mm-3.0mm thick, 200mm-1600 wide stainless steel and aluminum sheet. Flat size can be precisely
to 0.3mm, with paper film, diagonal accuracy, surface flat, with a long row of rack, single the longest straight size up to 10 meters. Two production lines with a full load of 500 tons / day
Precision slitting machine can process the 0.3mm-3.0mm thick, 200mm-1600mm wide stainless steel and aluminum sheet. This machine rolling seamless up cylinder, can be single and double-sided plastic pasteStrip, meet the requirement of fine high stand ards. Maximum line speed: 250m/min
Laser cutting Laser cutting
Laser cutting production line, imported from Germany, using the world's most advanced technology, the latest model (Trump 3040) has begun formal production, stainless steel processing thickness can reach 20mm, carbon steel processing thickness can reach 25mm, aluminum plate processing thickness can reach 12mm processing Range: 2000mm*4000mm.
Laser cutting production line, the introduction of Germany imported models, using the world's most advanced technology, the latest model (TRUMPF 3040) has already started production, stainless steel
Processing thickness up to 20mm, carbon steel processing 25mm thickness plate processing thickness up to 12mm processing range: 2000mm*4000mm.
Sheet metal processing Sheet metal processing